Excitement About Alcast Company
Excitement About Alcast Company
Blog Article
The Main Principles Of Alcast Company
Table of Contents8 Easy Facts About Alcast Company ShownExcitement About Alcast CompanyExcitement About Alcast CompanyThe 15-Second Trick For Alcast CompanyNot known Facts About Alcast CompanyExcitement About Alcast Company
Chemical Contrast of Cast Aluminum Alloys Silicon advertises castability by minimizing the alloy's melting temperature and boosting fluidness throughout spreading. Additionally, silicon adds to the alloy's strength and put on resistance, making it beneficial in applications where resilience is important, such as auto components and engine parts.It additionally improves the machinability of the alloy, making it simpler to refine right into finished items. In this way, iron adds to the overall workability of aluminum alloys.
Manganese contributes to the toughness of light weight aluminum alloys and enhances workability. Magnesium is a lightweight component that offers strength and influence resistance to aluminum alloys.
The 7-Second Trick For Alcast Company
It enables the manufacturing of lightweight components with exceptional mechanical homes. Zinc improves the castability of light weight aluminum alloys and helps manage the solidification process throughout spreading. It improves the alloy's strength and firmness. It is usually found in applications where elaborate shapes and fine details are needed, such as ornamental spreadings and particular automotive parts.
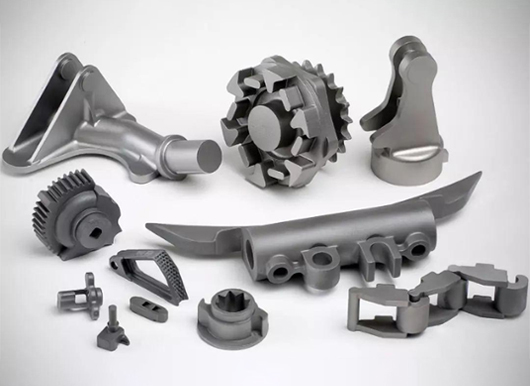
The main thermal conductivity, tensile toughness, return toughness, and prolongation differ. Among the above alloys, A356 has the greatest thermal conductivity, and A380 and ADC12 have the cheapest.
Alcast Company Things To Know Before You Buy
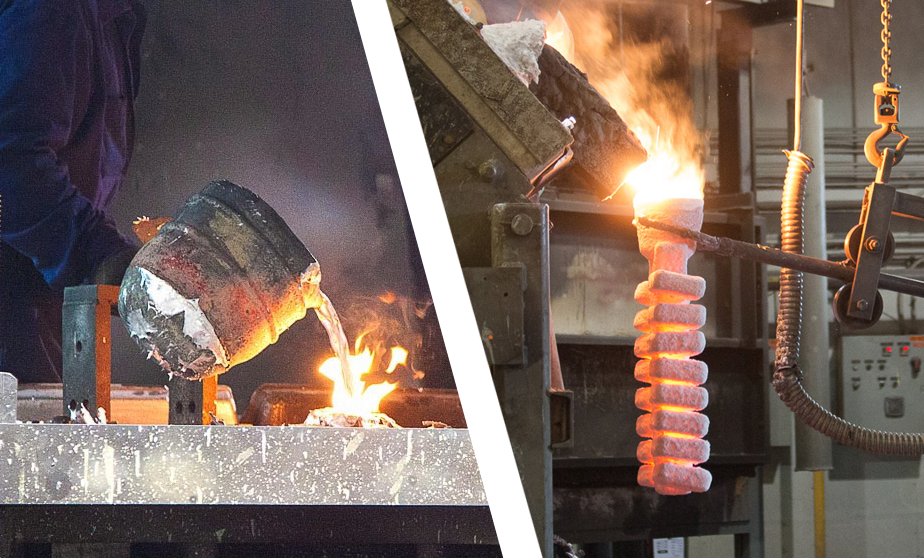
In precision spreading, 6063 is well-suited for applications where detailed geometries learn this here now and premium surface area coatings are vital. Instances include telecommunication enclosures, where the alloy's remarkable formability permits for sleek and cosmetically pleasing layouts while maintaining structural stability. In the Lighting Solutions market, precision-cast 6063 elements produce classy and efficient lighting fixtures that call for detailed forms and good thermal performance.
The A360 shows premium elongation, making it suitable for complicated and thin-walled parts. In accuracy casting applications, A360 is fit for markets such as Customer Electronic Devices, Telecommunication, and Power Tools.
A Biased View of Alcast Company
Its distinct homes make A360 an important choice for precision casting in these markets, enhancing item durability and quality. Casting Foundry. Aluminum alloy 380, or A380, is an extensively used spreading alloy with numerous distinctive characteristics.
In precision casting, aluminum 413 radiates in the Consumer Electronic Devices and Power Equipment industries. This alloy's premium deterioration resistance makes it a superb selection for exterior applications, making sure lasting, long lasting products in the mentioned markets.
Alcast Company Can Be Fun For Anyone
The aluminum alloy you select will significantly influence both the spreading process and the homes of the last product. Because of this, you should make your decision thoroughly and take an educated method.
Figuring out the most ideal light weight aluminum alloy for your application will certainly suggest evaluating a vast selection of characteristics. These comparative alloy characteristics follow the North American Die Casting Organization's standards, and we've split them right into two groups. The initial group addresses alloy features that affect the production process. The second covers characteristics impacting the buildings of the last product.
Alcast Company for Dummies
The alloy you choose for die spreading directly influences a number of facets of the spreading process, like how very easy the alloy is to work with and if it is vulnerable to casting flaws. Warm breaking, also referred to as solidification breaking, is a regular die casting flaw for aluminum alloys that can cause internal or surface-level splits or splits.
Specific light weight aluminum alloys are more vulnerable to warm breaking than others, and your option must consider this. One more usual problem discovered in the die spreading of aluminum is die soldering, which is when the actors adheres to the die wall surfaces and makes ejection tough. It can harm both the actors and the die, so you should search for alloys with high anti-soldering homes.
Corrosion resistance, which is already a remarkable attribute of light weight aluminum, can differ substantially from alloy to alloy and is a vital characteristic to think about relying on the ecological problems your item will certainly be exposed to (Aluminum Casting). Wear resistance is another building typically sought in aluminum items and can differentiate some alloys
Report this page